Forming technology of POM plastic gear
TIME:2021-9-28
She Zhangnan
Abstract: engineering plastics are widely used in various fields because of their light weight, good chemical stability, vibration absorption and noise elimination, high specific strength and convenient forming and processing. Taking POM plastic forming gear parts as an example, the main processes such as pressure, temperature and time in the forming process are technically analyzed, the process parameters meeting the production requirements are formulated, and qualified parts are produced, which provides reference for the industry.
Keywords: POM plastics; Forming process; Plastic gear
CLC No.: tq320.66
Process Technology for the POM Plastic Molding Gear
SHE Zhang-nan
ABSTRACT: Engineering plastics are widely used in many areas due to the characteristics of light-weight, perfect chemical stability, vibration absorption and noise reduction, high specific strength and convenience of forming and processing. The main processes, like the pressure, temperature, and time of the molding process, are analyzed technically based on the example of the POM plastic molding gear parts, formulating the processing parameters to produce the qualified parts and to provide reference for the industry.
Key words: POM plastic, forming technique, plastic gear
introduction
At present, engineering plastics are widely used in various fields because plastics have many characteristics that metal materials do not have, such as light weight, vibration absorption and noise elimination, high specific strength, convenient forming and processing, etc. [1]. However, the precision of plastic parts formed by mold is worse than that of metal machined parts. Therefore, when high-precision requirements such as cooperation relationship or precision transmission are required, it is necessary to strictly control the forming process of plastic parts, control the process parameters, and make preparations before forming and post-treatment of parts after forming, so as to obtain qualified parts.
1 product structure analysis
As shown in Figure 1, the gear is similar to disc parts. The die structure is relatively simple and the filling is not difficult. The difficulty lies in the control of tooth profile accuracy and the anti fatigue strength to meet the expected requirements. POM (polyoxymethylene) is selected according to the gear working environment. POM has good impact resistance and friction resistance. At the same time, it is a crystalline plastic. When the crystallinity is high, it will also have high hardness, which is very suitable for gear materials.
2 product forming process analysis
Gear forming process flow: raw material inspection, mixing, drying and injection molding.
2.1 raw material inspection
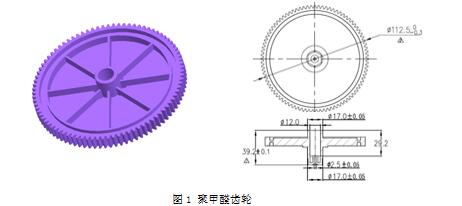
The quality of raw materials is the prerequisite for the smooth forming of parts, and also affects the determination of subsequent process parameters. It should be noted that the performance of different manufacturers of the same raw material will also be different, even for different batches of raw materials from the same manufacturer. Therefore, after the raw materials enter the plant, the basic performance test shall be carried out, such as fluidity, shrinkage, etc. [2]. During molding, the process parameters shall be adjusted according to the actual situation.
2.2 mixing
The general requirement for mixing is to mix raw materials and recycled materials evenly to ensure the smooth plasticization process. According to the application requirements and forming requirements of the gear, the proportion of return material shall be controlled within 10%, and the mixing time of the mixer shall not be less than 15 minutes.
2.3 drying materials
The moisture absorption of POM material is relatively small. Generally, parts can not be baked, but the gear precision is required to be high. In order to ensure the appearance quality and dimensional accuracy, the raw materials should be dried [3]. On the premise of ensuring that the parts are qualified, consider the production efficiency and shorten the drying time as far as possible. The drying temperature is 80-90 ℃ and the drying time is 2 hours.
2.4 injection molding
The process parameter setting of injection molding process is the key to whether the product is qualified or not. According to the characteristics of different raw materials and parts, the process parameters such as pressure, temperature and time during injection molding can be reasonably set to obtain qualified products. POM belongs to crystalline plastic and heat sensitive plastic, so the temperature should be strictly controlled during molding, and other process parameters should be set reasonably.
2.4.1 temperature
The melt temperature of POM shall be controlled within 220 ℃ generally, and it is easy to decompose if the temperature is higher than 240 ℃. According to the conventional setting method, first set the barrel temperature as: 170 ℃ for the fifth section, 180 ℃ for the fourth section, 190 ℃ for the third section, 200 ℃ for the second section and 210 ℃ for the first section, with a difference of 10 ℃ for each section. When testing the finished product, it is found that the hardness does not meet the requirements, and the analysis reason is that the crystallinity is not enough. Set the barrel temperature again as 180 ℃ in the fifth section, 190 ℃ in the fourth section, 200 ℃ in the third section, 210 ℃ in the second section and 220 ℃ in the first section. After testing, the hardness is improved. After the set temperature of the barrel is increased, the crystallinity during forming is increased, which is conducive to the improvement of gear strength and hardness. At the same time, the plasticizing efficiency is also improved, because POM is a crystalline plastic, plasticizing requires more heat, and because the condensation speed of POM is fast and the gear shape is complex, appropriately increasing the melt temperature is also conducive to mold filling and gear accuracy control. When the barrel temperature is increased, the mold temperature is also appropriately increased, which is conducive to the flow of molten material and obtain a good appearance. Higher die temperature is also conducive to the elimination of residual stress [4]. In actual production, the mold temperature is controlled in the range of 90-100 ℃ and the cooling time is 20 seconds. The cooling water channel shall be set reasonably to ensure uniform cooling as far as possible to prevent excessive internal stress from affecting the dimensional accuracy and appearance quality of products.
2.4.2 injection pressure and injection speed
Due to the rapid condensation speed of POM, it is easy to form defects such as weld marks and stripes. The use of higher firing speed is conducive to the molding of complex gears, and correspondingly, higher injection pressure should also be used. In addition, the viscosity of POM is sensitive to the injection speed and insensitive to temperature. Therefore, when it is necessary to improve the fluidity, it is also necessary to increase the injection speed and injection pressure. However, if the fire speed and pressure are too high, the products may form defects such as flash, jet and trapped gas, so it should also be controlled. The injection speed and pressure shall be set according to the wall thickness of plastic parts and the complexity of mold cavity. Generally, multi-stage injection is adopted, that is, different pressure and speed are adopted in different stages of injection and pressure holding to meet the requirements of different stages. In actual production, according to the requirements of slow fast slow, three-stage injection is adopted. The first stage injection pressure is 110MPa, the speed is 30%, the second stage injection pressure is 100MPa, the speed is 45% (the maximum speed of screw is 100%), the third stage injection pressure is 85mpa, the speed is 35%, and good results are achieved.
2.4.3 time
The molding cycle mainly includes injection time, pressure holding time, cooling time and mold opening and closing time. The shorter the molding cycle, the higher the efficiency and the lower the cost. Therefore, on the premise of ensuring the quality, strive to minimize the molding cycle. Many factors such as material characteristics, mold structure, injection pressure, speed and temperature will affect the molding cycle. The injection time can be estimated by the following formula:
Injection time = total glue injection / 40% maximum injection speed of injection molding machine + time base
The value of time base varies slightly according to the tonnage of injection molding machine:
< 200t takes 1-2 seconds; 2-3 seconds for 200t-500t; Take 3-4 seconds for 500-1000t. The estimated value shall be adjusted according to the finished product.
The pressure holding time mainly depends on whether the accuracy requirements of the finished product can be guaranteed. Insufficient or excessive pressure holding will cause adverse effects [5], especially for the gear of POM material, the products with large shrinkage and high accuracy requirements should pay more attention to the pressure holding process. It is difficult to accurately determine the pressure holding time. The type, quantity and position of mold gate have a direct impact, so they should be determined comprehensively according to the actual situation. The model of the injection molding machine used for the production of this product is the CNC all electric injection molding machine S80. The maximum injection speed is in the gear molding and pressure holding stage. The pressure holding pressure in the first stage is 85mpa, the speed is 25%, the pressure holding pressure in the second stage is 65mpa, the speed is 25%, and the pressure holding time in both stages is 2 seconds, meeting the plastic filling requirements of the product.
The cooling time shall be determined based on that the product is fully cured, has certain stiffness and will not cause deformation and cracking during ejection. Due to insufficient cooling, the product is soft and rigid, which can not bear the jacking force during ejection, and will deform or even crack. Excessive cooling will cause difficulty in demoulding and low production efficiency. Although there are some theoretical calculation formulas, there are too many assumptions. For the complex injection molding process, the calculated value deviation is large, so it is easier to obtain a relatively suitable cooling time by adjusting according to the actual situation. Through the die test, the cooling time of the gear is set as 20 seconds. The injection molding process parameters set for gear forming are shown in the table below.
Injection molding process parameters
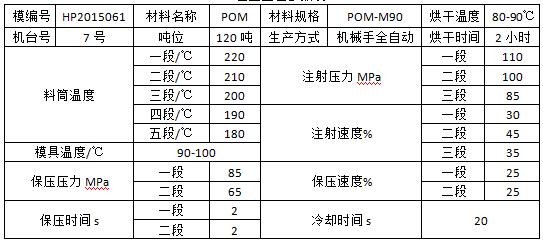
Die number
HP2015061
Material name
POM
Material specification
POM-M90
Drying temperature
80-90℃
Machine number
No. 7
tonnage
120 tons
Mode of production
Fully automatic manipulator
Drying Time
2 hours
Barrel temperature
First stage / ℃
two hundred and twenty
Injection pressure Mpa
a section
one hundred and ten
Second stage / ℃
two hundred and ten
Second paragraph
one hundred
Third stage / ℃
two hundred
Three sections
eighty-five
Section IV / ℃
one hundred and ninety
Injection speed%
a section
thirty
Section V / ℃
one hundred and eighty
Second paragraph
forty-five
Mold temperature / ℃
90-100
Three sections
thirty-five
Holding pressure Mpa
a section
eighty-five
Pressure maintaining speed%
a section
twenty-five
Second paragraph
sixty-five
Second paragraph
twenty-five
Pressure holding time s
a section
two
Cooling time s
twenty
Second paragraph
two
3 production verification
In the actual production process, after setting according to the above process parameters, the mass production quality is stable, meets the product testing requirements, and ensures the continuous and smooth production of products.
4 Summary
For POM plastic gear forming, on the basis of fully analyzing the product structure and comprehensively understanding the characteristics of POM materials, reasonably set various process parameters and adjust them according to the mold test. The conclusion obtained from the analysis of POM plastic gear forming process is also applicable to other similar plastic products with POM material, which provides a reference basis for the setting of process parameters of such products.
reference
[1] Feng Qin, Liao Hongyi. Research status and ideas of plastic molding size control [J]. Plastic industry, 2009, (7): 6-8
[2] Xu Zelin. Standardized mold test and process optimization method for injection molding [D]. Wuhan: material processing engineering of Huazhong University of science and technology, 2017
[3] Ben Keping, Meng Yuxi. Forming analysis and die design of automotive precision plastic parts [J]. Die manufacturing, 2008, (7): 41-44
[4] Xu Ao. Research on common defects and Countermeasures of injection molding process [J]. Research on agricultural mechanization, 2019, (lower February): 42
[5] Yao Wenlong. Research on Optimization of injection molding process parameters of plastic gear based on CAE [D]. Changsha: Forestry mechanization engineering of Central South University of forestry science and technology, 2015
About the author: she Zhangnan (1969 -), male, from Nan'an, Fujian Province, engineer, mainly engaged in plastic mold R & D and plastic part forming process research.